DMG MORI: Build Plate “Pucks” Cut Postprocessing Time by 80%
For spinal implants and other small 3D printed parts made through laser powder bed fusion, separate clampable units resting within the build plate provide for easy transfer to a CNC lathe.
Share
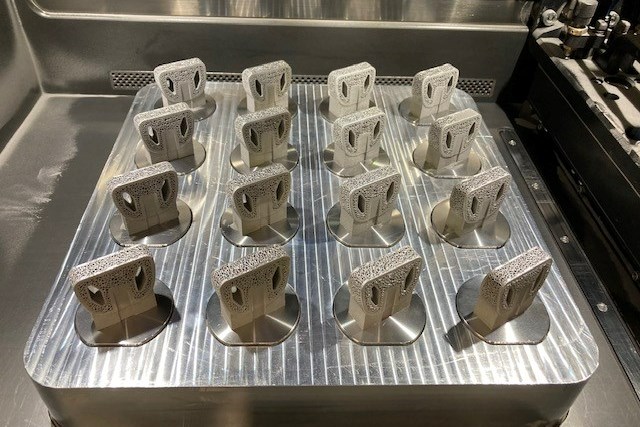
Parts are not 3D printed directly onto the build plate, but instead 3D printed onto pucks resting within the build plate. Downstream machining thus becomes much easier.
Could the key to an efficient additive manufacturing production workflow be found in the build plate?
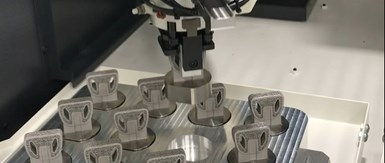
Among other things, the puck system enables robot automation. The robot tending a CNC machine tool can load the additive parts one at a time. This image and others in the article are courtesy of DMG MORI.
AM technology provider DMG MORI has worked with users of its laser powder bed fusion (LPBF) machines to implement a simple but significant change to build plates that streamlines production of small LPBF parts. Using modified build plates, parts are 3D printed onto separate round pucks that rest within the overall square plate. Each puck then travels with the printed part via robot loading into a CNC lathe, where the puck serves as the clamping feature for holding the workpiece in the chuck. With the part initially held this way, all CNC machining, including cutoff, can be performed in one cycle on a lathe featuring milling capability and dual spindles for complete turning of the part. That means no wire EDM is needed for part removal from the plate. It also means no build plate resurfacing is required, because the puck gets resurfaced via the lathe’s cutoff operation. DMG MORI says the process integration between 3D printing and machining made possible by the puck system, when applied to an additive build of 16 spine implants, reduces the total postprocessing time by 80% — from more than 6 hours for EDM plus finish machining down to just 1 hour and 20 minutes for machining with the puck system.
Lennart Tasche is additive intelligence consultant with DMG MORI Additive Solutions. He notes that the company is in a distinctive position when it comes to integrating metal 3D printing and machining: Beyond its AM offerings including LPBF and directed energy deposition (DED), DMG MORI is also long-established as a provider of machining automation.
“We want to improve the additive manufacturing process chain overall, and I think we are in a unique spot to do that,” Tasche says. “We have the machines and knowledge to bring automation to additive, to realize better process integration between additive and CNC. So, we are thinking: How can we move better from additive to subtractive? How can we make the total process leaner and faster?”
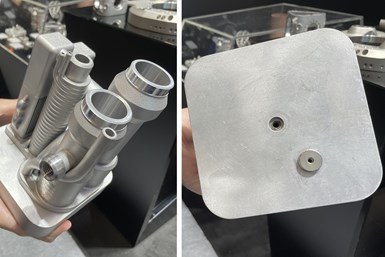
Here is a different system that has also been applied successfully for integrating metal additive with downstream machining. Zero-point clamping works well for shifting a workpiece from one CNC machine to another, and DMG MORI has also applied it for shifting an AM part like this one from the additive machine to a machine tool. This system needs a special receiver for clampling within the machine.
Some established technologies extend well to AM. For example, in machining, repeatable transfer from one machine tool to the next often relies on a “zero-point” clamping system in which clamping features on the underside of the fixture allows the fixture to quickly lock in place on multiple machines outfitted with the same receiver. For larger 3D printed parts, DMG MORI has applied zero-point clamping to its additive machines, allowing the part to go straight from LPBF or DED to CNC machining without setup time on the second machine. But for small additive parts, zero-point clamping is not the right fit, not just because of the space needed for the receiver, but also because the clamping force is not necessarily needed for 3D printing at the smaller size. Company engineers therefore expanded the process integration options that AM can employ. For smaller parts, the puck is in many ways an easier solution.
A Tray of Pucks

The pucks are simply machined build surfaces, resting in pockets in the larger build plate.
In this system, the puck rests precisely within a mating pocket machined into the build plate. Holding force is not needed. In LPBF, the forces tend to come from stresses within the parts as they grow, and the build plate in LPBF is secured to resist the cumulative effect of these stresses across the entire build area of the plate. But the potential distortion of a part as small as a medical implant is not enough to shift the location of one puck holding one such part. Therefore, gravity is sufficient to keep the puck in place, combined with a flat milled onto the puck to assure rotary alignment. The build plate then becomes like a rack or tray, holding these many pucks. In moving from LPBF to machining, the one manual intervention needed is removal of the completed build plate from the additive machine and placing this plate (with all its pucks) into a robot loading station. The robot can then lift pucks (with parts) out of the build plate for loading into the lathe one at a time.
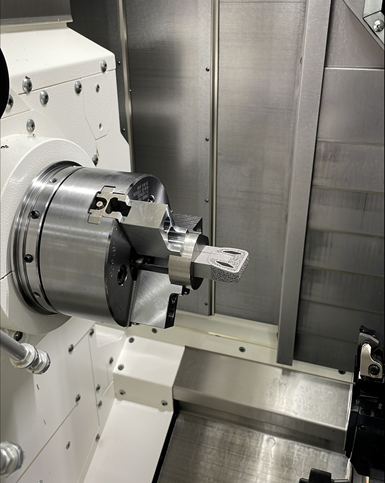
The round form of the puck then provides a perfect clamping feature for postprocess machining in a lathe.
Tasche says the resulting consolidation of AM postprocessing steps into one cycle represents a significant cost savings. The elimination of part removal from the build plate as a standalone operation is probably the chief example of this.
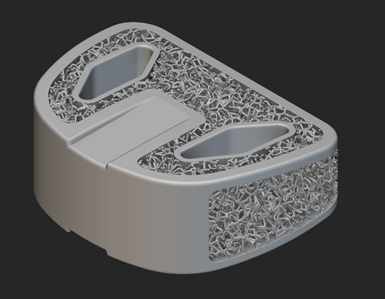
The implant itself is also designed to aid machining. The flat in the middle of this implant, along with the identical flat on the side below, allows for gripping by the lathe's opposing spindle, so that the puck can be machined away.
“Wire EDM, or bandsaw cutting — that’s a big step,” he says. “If wire EDM is needed, this takes time and the equipment is expensive. If the work is done with a bandsaw, then there is more work to remove additional supports and resurface the plate. The chance to do away with all this can be a relief.”
Plus, through a compressed air or coolant wash step, powder removal can be made a quick and automatic part of the same machining cycle as well.
One final compelling feature of this approach to additive/subtractive integration is the extent to which the idea, because it is so straightforward to implement, is both adaptable and scalable. The solution is being applied now by DMG MORI customers using “pucks” that were cut from round barstock. But pucks for future applications could be a different size or shape, as the application calls for. Unlike zero-point clamping, says Tasche, this idea will not require the company to stock or support any special hardware — the idea can advance just by teaching it to potential users. “Every manufacturer that has machining, and wants to integrate it with additive, should already have the capability they need to machine their own build plates and pucks,” he says.
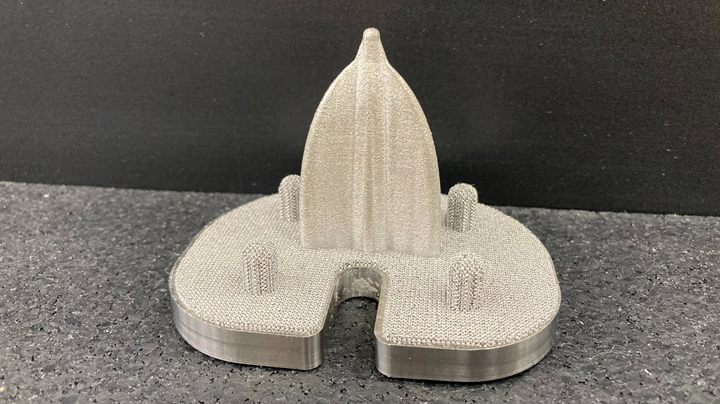
The puck could even simply be machined to a geometry that allows it to become a section of the final part, rather than being cut away. That was the case with this knee implant. The build surface (and the associated pocket in the build plate) were machined to a shape determined by the required form of the component, meaning not all of the part was made additively.
Related Content
Possibilities From Electroplating 3D Printed Plastic Parts
Adding layers of nickel or copper to 3D printed polymer can impart desired properties such as electrical conductivity, EMI shielding, abrasion resistance and improved strength — approaching and even exceeding 3D printed metal, according to RePliForm.
Read MoreNew Zeda Additive Manufacturing Factory in Ohio Will Serve Medical, Military and Aerospace Production
Site providing laser powder bed fusion as well as machining and other postprocessing will open in late 2023, and will employ over 100. Chief technology officer Greg Morris sees economic and personnel advantages of serving different markets from a single AM facility.
Read MorePostprocessing Steps and Costs for Metal 3D Printing
When your metal part is done 3D printing, you just pull it out of the machine and start using it, right? Not exactly.
Read MoreWhy AM Leads to Internal Production for Collins Aerospace (Includes Video)
A new Charlotte-area center will provide additive manufacturing expertise and production capacity for Collins business units based across the country, allowing the company to guard proprietary design and process details that are often part of AM.
Read MoreRead Next
Why Robots and Additive Manufacturing Go Together
3D printing and robots enable one another. We miss the possibilities of one if we do not consider the other. The combination includes AM for end effectors, robots for 3D printing parts, and different modes of metal and plastic production.
Read MoreAutomated 3D Printing at Evco: Composites, Cobots, Email and More
Injection molder Evco has long seen the importance of industrial automation for plastics processing. Its latest automation feat? A cobot-tended cell of 3D printers for manufacturing fixtures and customer products unattended.
Read MoreVideo: Intelligent Layering Metal 3D Printing at 3DEO
Contract manufacturer 3DEO delivers metal parts using Intelligent Layering, a binder jetting-like 3D printing process the company developed and operates internally. Here’s how it works.
Read More